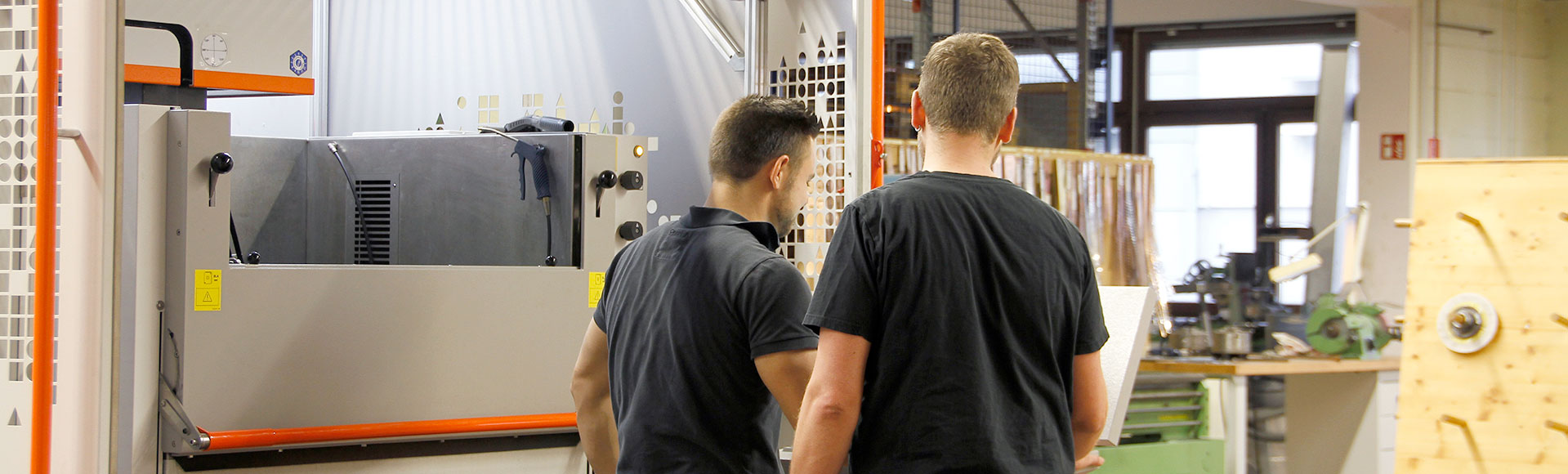
Toolmaking for high-precision stamped parts
In our toolshop we manufacture
high-performance precision tools and progressive tools
for small, medium and large series
for single or multiple falling parts
from tool steel or carbide
for one or several cycles
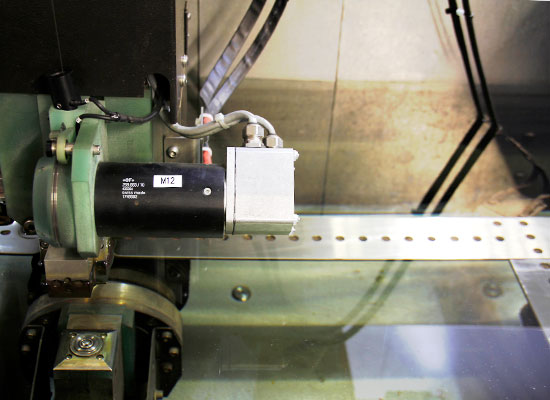
Our continuous process chain includes development, construction, production and erosion in 3D. To do so, we use the software program Visi Cad as well as the 3D viewer. To ensure a smooth process during tool production, all relevant departments, including toolmaking and stamping as well as quality assurance, are involved from the start of the project. The prototypes are designed according to your individual requirements.
The optimum process
Design
During the design phase, all departments involved in the project also take part in planning. Thus, you benefit from quick and precise processes. This early stage of toolmaking is where we integrate our zero-error plan, thereby ensuring optimum effectiveness.
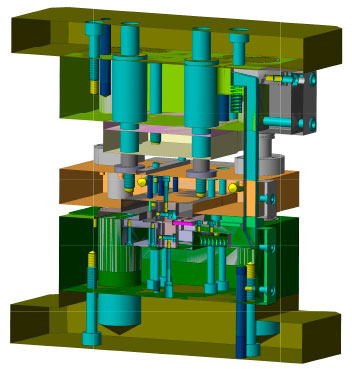
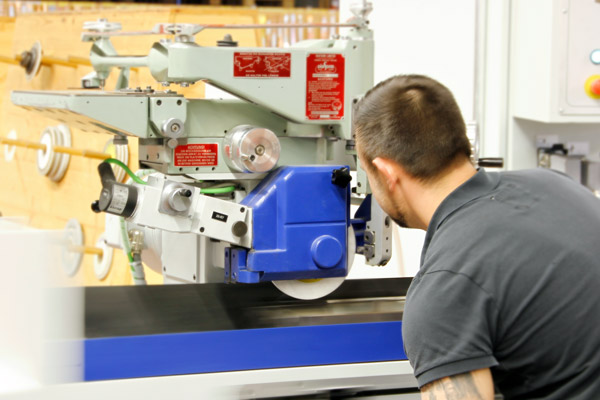
Single-unit production
Once a detailed plan has been developed and any sources of error excluded, single-unit production can begin. Our fully equipped machines enable us to implement the entire value-added chain on our premises, from the initial machining and curing, eroding and milling up to the finished part.
Toolmaking
The individual production parts, which can be very complex, are assembled step by step by our qualified employees. The various components of the high-precision tools are produced based on CAD data and drawings and coordinated as a unit – these tools are accurately milled and pave the way for the manufacture of your stamped products.
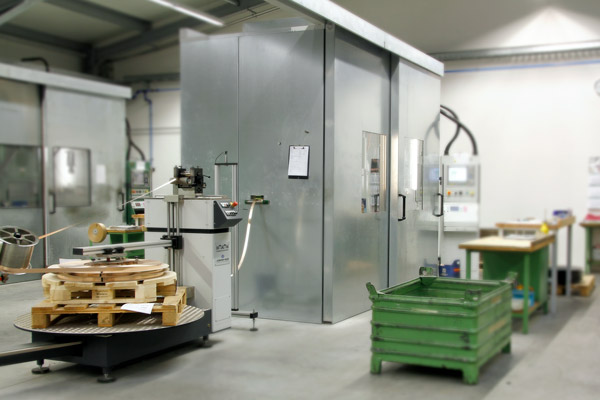
The prototype is constructed together with you before it goes into series production. It is tailored to your requirements and offers the opportunity to optimise the quality and approve the tool. After you have given approval, series production begins.
In order to achieve a top-class standard consistently and therefore meet all the expectations of our customers, we document quality on an ongoing basis. To do so, we use the Production Part Approval Process (PPAP) with its comprehensive requirements as well as documentation and approval stages.